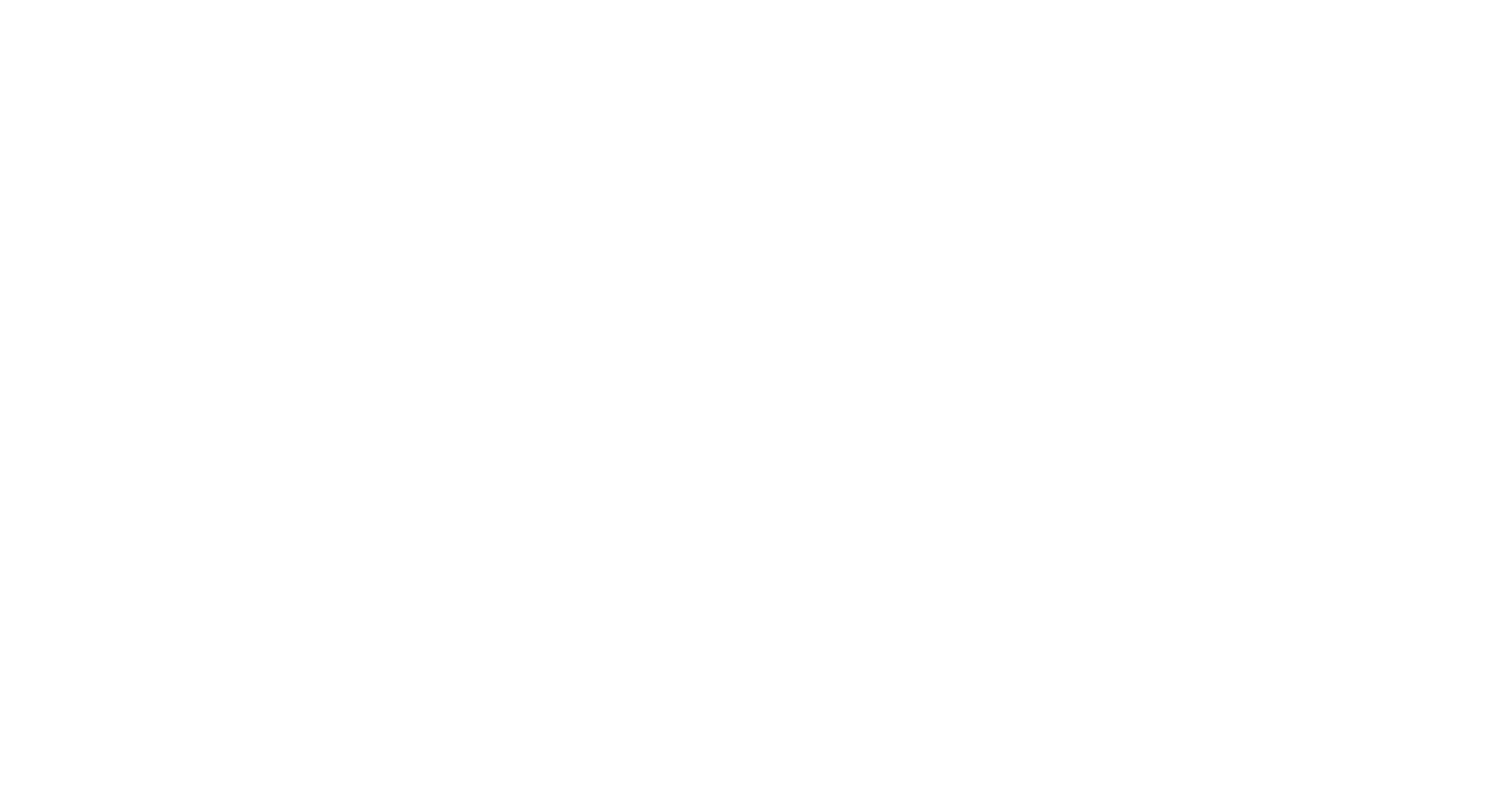
SuperTeox
Members-
Posts
21 -
Joined
-
Last visited
Contact Information
Recent Profile Visitors
The recent visitors block is disabled and is not being shown to other users. |
-
End-of-February update: modified the engine crankcase to increase the oil capacity to 450ml by moving the ventilation intake behind the starter shaft (don't tell me about anyone who first closed the clutch cover with the starter return spring stuck 🤬😞) the wall is thin so I thought of threading the hole m5 and using a bit of loctite, it's much better than hammering it in: threaded the original ventilation hole to m6 and added a stainless steel screw with a copper washer: modified the gearbox plate by drilling a 4mm hole at the bottom right to allow oil to pass better on the left: Water pump overhauled: a small puller on the gear is enough to free it from the shaft, behind it there is a circlip and everything comes away magically: used a Gas Gas seal instead of the original one which has a double lip and is perfectly compatible: MT280210020 10x35x7. install backwards, you don't need as much pressure to insert the gear into the shaft, be very careful when handling the seals especially when sliding onto the shaft! unfortunately I'm still waiting for bearings and thinking about how to fix the gearbox so I moved on to cleaning components and finishing dismantling the frame: here I was really lucky, thanks to the €35 puller on Amazon (the best money spent ever), first removed the bearing rollers mounted on the plate and then using a piece of soft aluminum (be careful not to ruin the thread of the steering column) I pulled the bearing race. for the frame I used a slightly bent iron rod and knocked out the bearing race using the 3 grooves in the frame I'm almost certain that it won't go so well on my Explorer, too lucky 😁😁😁 I was thinking of using Motorex Trial Gear Oil 75W... isn't that a good oil?
-
Thanks for the information on the drum, so just remove any residue that could come off and put it back on.. I just need to fix the starter gear and I should have everything to reassemble the engine. I also noticed from the pics on your website that your Easy Start is different.. I wonder how many versions there will be. 😁 However the wires were not welded well, easy to get a few shorts..
-
When I finished the '12 I think I'd completely disassemble the '14 so I can have a bit of fun, even if it's in perfect working order, I prefer to start again from 0 hours, I'm already buying some spare parts around
-
few more updates: removed the ruined bushing from the crankshaft to make the modification to the plate with the ball bearing: After a few attempts there was nothing to do, I took the Dremel and made a path to be able to take it with the puller. You need to heat, it's really tight on the crankshaft I started to clean everything and create a few 3D printed parts to insert the seals and bearings: I also disassembled the gearbox, I recommend you to follow this forum thread: Unfortunately, however, both the starter gear (also the counterpart on the starter shaft) and the gear drum do not seem to be in great shape at all: trialshop has available both the drum and the gear on the shaft, I tried to contact Lamfos for the starter gear but unfortunately they are no longer produced and they don't have any more... If you have any info it would be great! I'm also thinking of upgrading the crankcase and moving the ventilation pipe, to be able to use 450ml of oil instead of 350, it's the perfect time to do it since it's all disassembled and you just need to make a hole Looking through the things that the seller of my Explorer '14 gave me incredibly I found this: After a bit of cleaning work, unsoldered everything, resoldered, fixed the cables, here it is: Fully functional (I don't know why it was in that condition), I change the battery and capacitor and I think I'll update the electrical system of the '12 Explorer to mount it the kill switch input is controlled by the PIC which controls the 30 seconds of operation of the step-up power supply and after passing 2 diodes it is sent back to the ECU The pick-up from the flywheel passes through an optical transistor that activates the system It would also be easy enough to replicate as a circuit, but big payoff this time!
-
small update: Sister found near home to be saved, it's a 2014!
-
I think that at this point, given that it has good tolerances, I won't open it, it's still an operation that stresses the materials, for me it's the first trial engine I've rebuilt so I'll follow your advice if they actually aren't as stressed as a MX tried to figure out how long the TXT conrods are but I couldn't find this information, it would be interesting to find out which connecting rod it is, I saw that trialshop sells the complete "original OSSA" kit thought about how to measure the conrod mounted: less pin/2 , plus hole/2 make "circa" 118mm. before reassembling the engine I take all the measurements of the crankshaft and put them here with a centesimal analog comparator you have a definition of 0.01mm per division, when you turn the crankshaft you can see the needle moving within a division very well, sure 0.005mm is approximate but you can understand if it moves almost half a division looking at some specifications of 2-stroke engines it's not bad to stay under 0.01mm of runout
-
I checked the freeplay at the little end of the conrod and it's 0.42mm ~ 0.45mm without applying too much force at the highest point, it shouldn't be bad!
-
is 0.005mm. You're right I forgot to check the freeplay at the top, tomorrow I'll check My sixth sense tells me to open and change the bearing anyway but it involves a lot of work and above all I am confident about finding the bearing but I would have no idea about the pin. I haven't been able to figure out if it's a connecting rod of some existing bike or if it was custom made (there is no gas gas logo on the connecting rod and no code)
-
I need an opinion on the crankshaft & conrod: - conrod has Zero radial play. - big end axial play 0.55 mm pass 0.60mm no pass - big end bearing runs well without noise or visual defects - conrod has NO color marks due to some heating - just tested the truing with two dial indicators (without the main bearings) and it has a runout of 0.5 cents. I think the tons of oil have preserved the crankshaft and I'm undecided what to do. Do I separate or not separate the crankshaft to change the connecting rod bearing?
-
incredibly I found this on https://trialshop.it/cuscinetti-motore/122893-cuscinettoparaolio-arancio-motore-dx-ossa-tr280i/ and all the gaskets! I have no idea if it is original or not but it already has the machining for the fixing pin and comes with a viton seal to be changed It doesn't come with O-rings but I think that at least the internal one on the shaft should be put, I found a good quantity of oil here; I don't know about the external one on the crankcase, it's much more difficult for oil to pass there regarding the O-rings of the head I followed a discussion here on the forum and I bought the Gas Gas ones: Internal Oring PN M01619215 External Oring PN M01619135 and also for the water pump seal I use the gas gas one which has a double seal PN MT280210020 yesterday evening I measured the cylinder and incredibly it is still 76.00 mm in the upper part and 75.99 mm in the lower part under the ports while the piston (it is a 75.95mm vertex) has dropped to 75.92mm. I believe that the tons of oil that was leaking kept the cylinder in good condition... already found an original 75.95mm piston on nonstop which I think is fine given the non-wear of the cylinder. I also found an internal plate PN 54-3400020213 of the 2014 model to see if I can switch to ball bearing on the left side. the idea is to take a 6205 bearing and replace the grease with the Kluber Topas Isoflex NB52 which is used successfully (if every 2 or 3 years you change it) in rotax skidoo engines (it is also very easy to change this bearing) now it remains to open the crankshaft and check the connecting rod and connecting rod bearing.. hoping it is a "normal" size
-
And here's who was probably leaking oil. Judging by the condition of the bearing, a 2-stroke engine has just been saved! 🤣 NO Orings found on the bearing, should there be?
-
After taking out the gearbox and taking a quick look where I see the drum and the idler gear probably in bad shape: I disassemble the cylinder by removing the four screws at the base and remove the piston. the cylinder is not bad at all, there are a few lines in the nikasil but nothing that you can feel with the nail, piston in good condition no sign of seizure only vertical lines probably from dirt pulled in in intake; Once the engine has been disassembled, I will try to measure them to see how they are worn out: The connecting rod doesn't seem to have vertical backlash but the main bearings don't seem to be in great shape, they make a lot of noise. I proceed to remove the inner plate on the magnet side with an puller using long M5 screws (in the photo I didn't have M5 but I rethreaded some M6) the seal seems ok but I realize that 2 small Orings are missing (do any of you gurus remember if they are really there?) could they be the cause of the oil leak? I realize that the crankshaft has an huge clearance almost 2mm lateral, a sign that the bearing on the right is definitely gone and I decide to completely extract the crankshaft from the crankcases to pull I used what I had in the workshop, a minibike rim, a 3D printed centering ring, a 1cm thick plate and an M12 bar that I threaded 3cm long M10x1.25 which is the thread of the flywheel screw; It is necessary to heat the bearing housing from the outside with a heat gun to avoid the risk of ruining the crankcase by pulling too much Once the crankshaft has been removed from the crankcase, it is necessary to first remove the gear from the shaft in order to be able to free the bearing. The tricky part is to remove the gear, it takes a good puller and heat up a lot (not with a propane torch). with my puller I managed to take the bearing in the Oring slot and in 2 seconds I pulled out the bearing:
-
ENGINE DISASSEMBLY: After removing the water pump by removing the three screws that secure it to the crankcase and the coolant hose I removed the head to see the condition of the piston and cylinder: ok it would seem that the gearbox oil has been leaking into the cylinder for a long time, really a lot of buildup but both the head and the piston don't look bad. I removed the magnet side cover and removed the flywheel with a M27 x 1 right thread Puller. removed the coils but there is no trace of fresh oil here, it looks more like an old leak Switch to the clutch side and gearbox removal; I remove the clutch cover and remove all the screws holding down the disc spring and remove the clutch assembly (a lot of metal flakes here): The clutch baskets remain integral to the gearbox and just remove the 5 screws (3 are hidden behind the clutch baskets) with a 3mm Allen key..... Ok..... simple! If only Godzilla hadn't locked them up! A screw gone (I would really like to talk to the inventor of the 3mm Allen key 🤐) and after two hours of testing, decided to drill the screw. Mission accomplished without disintegrating everything. ok once the screws have been removed, just hammer lightly on the pinion shaft and the gearbox comes out of the crankcase.... maybe... After a day of trying and a pack of cigarettes, I decide to remove the vent plug near the pinion shaft and realize that behind the bearing there is the locking shaft!! with a 3mm hole!! (Konrad there is the fourth version of the locking shaft!) I removed the bolt inside the clutch basket (Be careful it's a reverse thread!!) with an 3mm Allen key (🤣) inside the ventilation hole and the gearbox came off with a couple of taps.
-
SuperTeox started following 2012 Explorer 280i Rebuild
-
Hi everyone, as promised i'm sharing the entire 2012 Explorer 280i project to provide as much information as possible to those who need it. Here is the bike before complete disassembly: The bike starts (with difficulty) has good compression (forgot to test it before opening the engine), the gears are ok (neutral doesn't go in easily), the engine's electrical system works but nothing of the Explorer's additional system works; A 12V battery with flying wires that activates the pump and ECU has been added by someone previously. The engine runs very very rich and makes a lot of smoke (the locomotive from Back to the Future III makes less smoke) Before disassembling the bike i read all the various discussions on the forum and looked for as much information as possible (Thanks Konrad and your https://www.ossa-efi.com/) to understand how to act and what to look for before completely disassembling it. After connecting the bike to K-scan (Thanks Lotus54) i managed to test the various sensors and discovered that the motorbike has 300h (assuming is the original ECU) and find the only one that gives wrong values is the engine temperature sensor (23°C instead of 11°C ambient with the bike stopped for weeks) The time to dismantle the back of the bike, the exhaust, the shock absorber and the swingarm and... first problem! a crack in the rear swingarm link! ok, let's look for the spare part later hoping to find it. Removed the additional tank (cool the quick no leak disconnection fitting), some electronics, removed the lower plate (there are some electrical connections in the front behind the plate stuck by the engine, just under the fuel pump), the reed valve and all the connections to the engine and here is the engine on the workbench (be careful not to pull the fuel hose that goes to the pump, the connection is weak and made of plastic) For the moment leave the remaining parts of the motorbike assembled and dedicate to completely dismantling the engine to understand the conditions and possibly look for spare parts.
-
Ok, I'm sure the connection works, I tried with a GasGas KSCAN but evidently it doesn't recognize the control unit.. However, looking at the transmission, it responds with the code of the control unit, so perfect