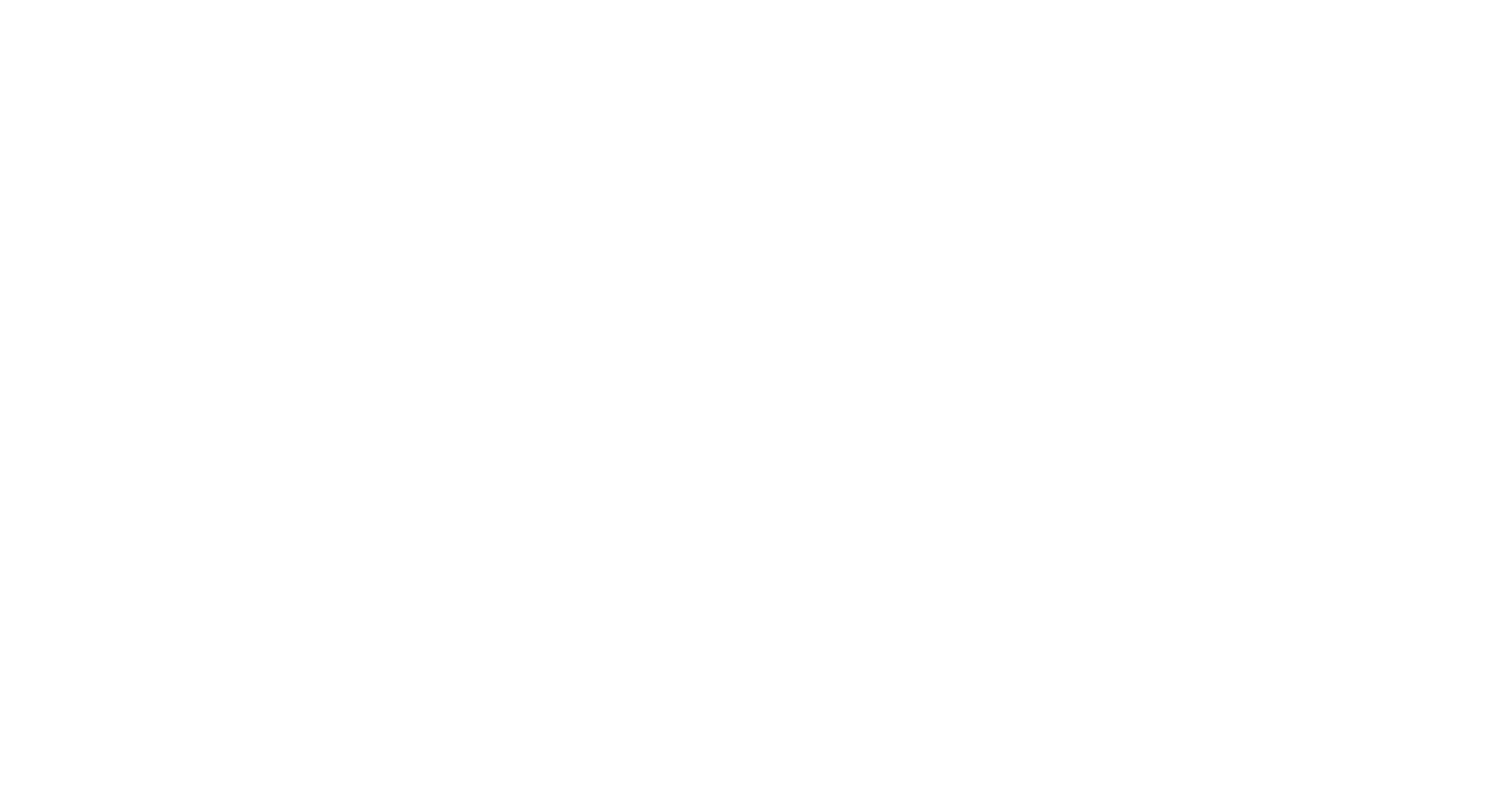
Tillerman6
Members-
Posts
328 -
Joined
-
Last visited
-
Has anyone tried the Moose Racing shift lever on their 74 TY 250 A? https://www.denniskirk.com/moose/blue-forged-shift-lever-for-husqvarna-tx125-2017-1602-1139.p579997.prd/579997.sku Let me know if you like it/ fits perfect or whatever- I'm probably going to replace mine soon cause it does not fold and is not stock anyway.
-
I think it's possible to put a TY piston into a DT 250, but not the other way around. The TY piston skirt is wider next to the flywheel circumference for the larger diameter of the TY flywheel. I think the diameter on the original TY 250 A piston is 69.96mm I don't know if Wossner makes one in that diameter. It's interesting to know that the wossner wrist pin is lighter than the stock Yamaha wrist pin- I might go with wossener next time around when I need a 1st or 2nd oversize. The CMSNL stuff is going for a premium.
-
The only direct replacement for a TY 250 piston- Yamaha OEM is from CMSNL. They are not cheap. I don't think Wisseco makes a direct replacement either. The DT 250 pistons will not fit without modification as the piston skirt shape is different and the weight of the piston is heavier than the TY 250 piston. I went thru this whole scenario recently and had to get CMSNL to send me a genuine TY 250 piston after they sent me a DT 250 piston with a skirt that hits the flywheel weights. If you are not replacing the con rod, you will have to go with the stock piston anyway, as any changes there will make it necessary to change the piston too most likely.
-
Guys- as you probably know, the stock air filter is not the easiest thing in the world to service or maintain. It worries me that the air box and air filter may allow dirt to enter the carb because of a poor fit and or leaks. Has anyone come up with a fix for the stock air filter problems? Here is the filter I'm using: https://www.ebay.com/itm/401499859787?hash=item5d7b41ab4b:g:9QMAAOSwnHZYUUUz It fits over a cage like this: https://www.ebay.com/itm/274750021130?hash=item3ff8609e0a:g:SYAAAOSw7wJgbfOe If you have found or made something better, please let me know!
-
The fuel I use is fairly fresh about 2 weeks old, but the plastic jugs I put it in may have gotten saw dust in one of them at some point in the past because I use the same mixture for the chain saw, and that jug is probably pretty dusty. The gas tank on the bike has fairly fine screens in it and they are clean and intact, so I just filtered the same fuel thru two coffee filters and put it back in the rinsed out fuel tank. I think I will put in another new air filter and get the proper air filter oil this time that is made for the air filter brand I'm using. Since I didn't find anything in the fuel tank to speak of its hard to say whether the culprit is airborne or from a dirty fuel jug. There was the usual dust around the fuel tank cap gasket, but nothing like that was in the carb float bowl drain plug recess. It looked more like sawdust if I had to make a guess.
-
Took the tank off and cleaned it and the fuel petcock. drained the mix and filtered it thru coffee filters- not much dirt or debris in the tank. The fuel filter is one of those very small clear cone shaped types and it did show about 10% of the surface area having something stuck in it. The flow arrow was correct. Question- if there is debris in the float bowl drain plug recess, is that strong evidence that the contamination is from the fuel itself, or is it still possible that there is some problem with the air filter?
-
I keep finding dust/dirt or sawdust in the float bowl drain plug. This can't be a good thing or normal. The fuel filter is inline, but is not stopping this contamination. I guess I'll have to investigate the main tank and it's filter, the fuel source container and the whole picture.
-
So today I changed the main jet down to a 112 and re- peaked the idle air bleed screw. I think it's running better now, but still going to see the guru tomorrow.
-
I hope he can tell me one way or the other. I only have the one bike and nobody around me has another one that runs, so it is hard to tell if it's normal or it could be much improved.
-
As soon as I get a chance I'm going to take the bike to a TY guru here locally and see what he thinks. Maybe I can ride one of his TY 250's and see if it does the same thing.
-
I think you can just disconnect the "boost switch" on there if it is in your way, but you would want to check with Rex's to be sure. The standard model seems to give the TY 250 about as much advance as it could ever use. I don't really need a lot because I run 99% of the time at lower rpm's and throttle settings.
-
Sorry you had trouble with the ordering. I did everything online and did all my guesswork as to which variety to order myself. The rest was just the paperwork, so it was pretty stress free. I went out and gave the bike a good work out today on some single track in my area of North Idaho. Met up with a new friend and he he led me up some single track switch backs going up hill in some loose rocks and tight turns- you had to keep some momentum up to stay on the trail and the ignition was great stuff. Most of the trail you could use fairly low rpm's in 2nd or 3rd and tractor up the hills with ease. The tight stuff was trickier as 2nd seemed too fast and first was too slow. Anyway we had a great time and no body got hurt, and if the ignition works as well in the future as it did today, I can say it was worth every cent I paid for it. By the way- thanks for the reply!
-
So this is just an update on my install and first tests of the Clubman ignition from Rex's Speed Shop. I was not sponsored, so this is on my own nickel. This kit has actually exceeded my expectations and I am very happy with the results. The install is very simple and most of the pictures are easy to understand. The first part of the install is to remove the magneto rotor with your special puller tool., swap out the old ignition back plate with the new one and bolt it down with the new hardware provided. I used a little blue Loctite on the three screws just for a little peace of mind. The new ignition plate is way less busy than the stock one as it does not have a lighting coil. I believe that is an option you can get when you order initially or possibly it can be added later if you need lights on your bike. This kit uses the original mag rotor, so the next step has you re- installing that again over the new coil assembly and torque things down to factory specs. The nut on the TY 250 A uses a hefty 50-55 foot pounds of torque on that nut, so special tools are a plus to have here. Next you are on to the mounting of the high tension coil and the new plug cap. I was much impressed with the fit on the HT coil as it was a snug fit into the TY 250 A frame with no modifications needed! I have seen several other kits being installed on You Tube video's and most of them require welding or new brackets to be fabricated for the HT coil- not this one! It slides in perfectly and bolts down with the original hardware! Very nice! With all the original wiring from the old HT coil removed, the only connection to make for my bike was one wire to the kill switch. This was done by adding a male bullet connector on to my old kill switch wiring and plugging that into the orange wire from the new HT coil. The other ground wire from the kill switch grounds to the mounting bolt where the HT coil also grounds to the frame. The last part of the install for this kit is the CDI module- this lives inside the TY "tool box" area, so if anyone was actually using the "tool box" for tools, they will have to find a new home for this install. The CDI box is small enough and mounts inside the tool box with velcro tape. The fit is fairly snug, so I feel as though it should stay in place well enough if you clean the inside surfaces first before sticking the assembly inside. Lastly, the wires are all connected and zip ties applied over the wiring harness covers- making sure not to apply zip ties directly over the wires and you are done! Just for fun I decided to see what kind of spark I was getting now with the new kit installed. - The plug threads were grounded to the frame and the kick starter produced a decent spark on about the 3rd kick. I think the circuits are not charged up until this happens since there is no battery in anywhere in the system. At any rate, it made sparks, so the plug was screwed back down and it was time to fire it up! I was also interested in knowing if there was any tendency to "kick back" on the start up proceedure as I had so often experienced with the old points system- So far - none of that has happened, so I am very happy about that as it was the main reason for upgrading to the new kit in the first place. I have only had the RSS system on the bike for 2 days now, so I can't give any long term reviews, but the fact of having a true advance curve seems to enhance the low speed handling of the bike. This may be just dreaming, but the slow turns with no clutch being used seem to take less effort and the bike rpm's are a little smoother overall. I have to say here that I am no trials rider by any stretch of the imagination, but I feel like the addition of this kit by Rex's Speed Shop is a definite improvement if for no other reason than the fact that you will not be crawling on the shop floor peering thru a tiny hole in the flywheel any time soon trying to set the points position relative to TDC ever again! Rex's does recommend going to a different plug for this kit- one of the new Iridium variety from NGK, so I did order one yesterday, and when it comes in it may enhance things slightly more, but I think today I'm going to go give it a try as is while the weather holds out. If anyone else has a Rex's Speed Shop kit installed- please let us know what your' experience was like! Tillerman6
-
Follow up- The OKO is running now and so far I've only made a couple of small changes. the pilot jet is changed down to the smaller size that came in the kit and the needle is dropped down 1/2 step with the tiny washer . I think these changes were needed because of the higher altitude I have than the OKO distributor. I'm at 2100 ft and they are at 700 ft. I was able to use the same cable kit parts from Venhill for the throttle cable and the throttle end is soldered on with regular electronics solder and flux. The throttle itself is the Domino slow throttle and the overall length of the cable is 49 inches. I did not measure the outer cable housing as it is in segments so that the cable length adjusters can be used. I am not in love with the standard air box for the TY 250 A. So I hope your efforts turn out better than that. But as weird as that thing is, it would be pretty difficult to replace and still have all the features that it has. i guess the biggest ones are that it is part rear fender, - splash resistant, holds the air filter, and incorporates the fitting for the special air pipe leading to the carb. So if you change any of these items or try to move them, it will change everything else and it will not be easy to do. However, I do hope you will post some pics of what you do and I might still be tempted to copy your efforts if they are successful. The Mid-Atlantic Trials website has an accessories page that lists several options for air filter products that adapt to the various OKO carbs, and they are all simpler than the stock arrangement, being so light weight and just mount with a hose clamp, but I'm not sure of any details beyond that. It would be really nice to simplify the air filter and do away with the stock air filter arrangement altogether, but I have not seen anyone do that and still have an air box around the air filter to protect it from water and mud. Best of luck and please keep us posted!