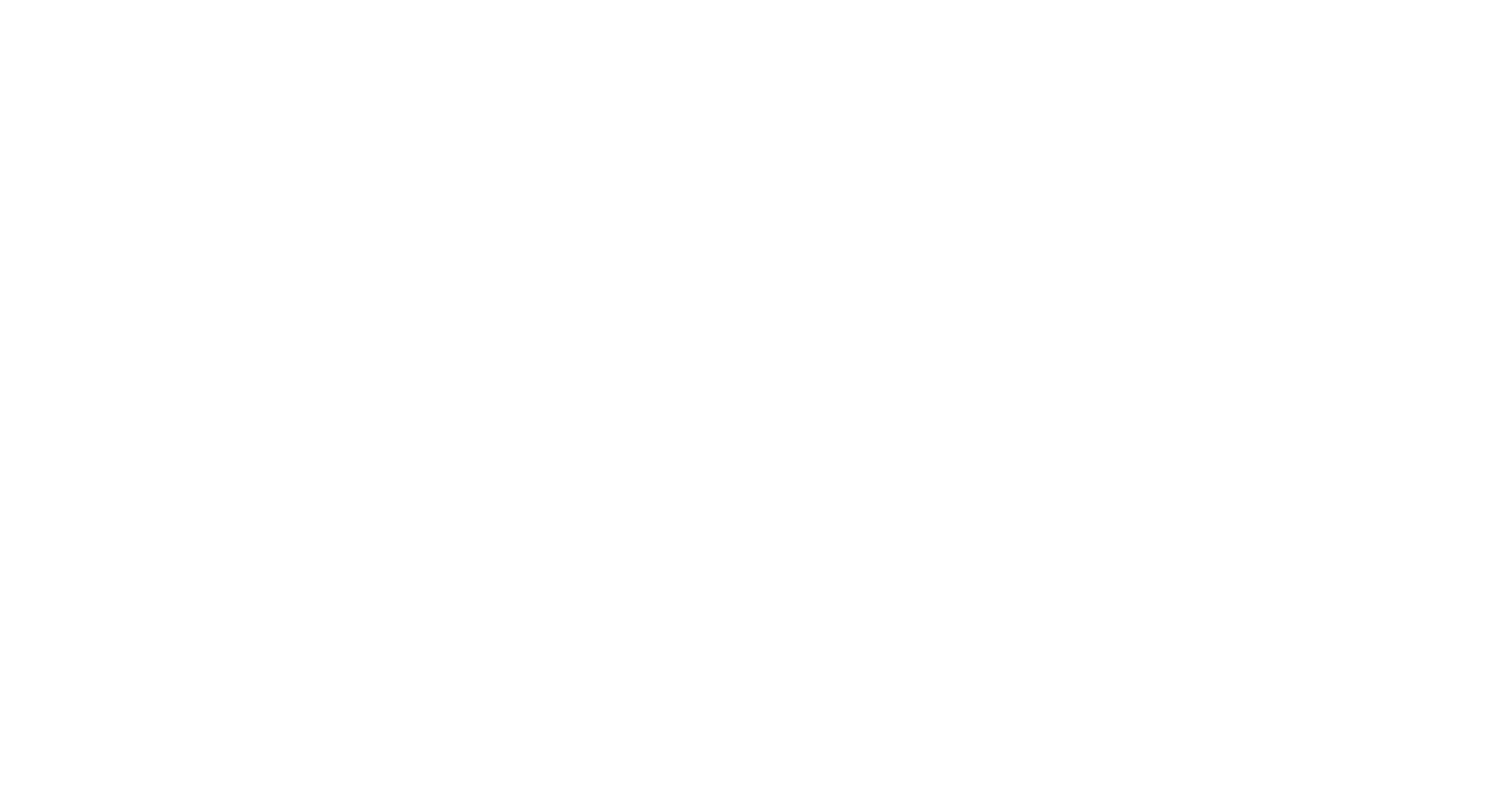
gwhy
Members-
Posts
590 -
Joined
-
Last visited
-
brushed tec if very old tec but also very easy to understand. brushelss is a much better/lighter tec but very hard to get to grips with if you not have a understanding of how they work, Price is comparable to be honest as controllers are much better spec/priced now than what they were 2-3 years ago, brushelss motors however can be a mine field to source one that would be suitable for a given application they are not cheap enough to take a gamble unless you know what you are looking for.
-
it dont look like a temp sensor. the temp sensor is in the motor ( I believe ) it is also there for a reason, main reason is to stop the motor burning out by limiting the power and not just to limit the power.
-
yes supplying a voltage directly to the motor will/should run the motor, just be careful supplying the full 48v as it will make the motor jolt into action quite violently,, better to test will a lower voltage i.e. a 12v battery. When I have tested older oset controllers they work without a relay in the system but the controller on the 24 maybe different, I would check the throttle/connections as long as the motor works after testing also on the diagram there are 2 fuses and a diode it would be worth testing these items before going any further, but if still no joy then you may need to email oset and ask them what the possible cause can be..
-
the reason i asked about the relay is on the smaller osets if the motor is open circuit at power on then the controller do not initialize I don't know to much about the 24 but i would not mind betting that it will be the same. I can not see any real reason for the bike not to work by bypassing the relay ( has anyone got a wiring diagram for the 24 ?), connecting the to fat red wire together was correct to bypass the relay. it still could be a initialization problem with the controller, you could try and un bypass the relay first then connect battery, turn key, then bypass relay just to see if this has a different effect. If not then a diagram will be only way to see what is going on.
-
what made you think the relay is bad is the first question ?. what wires did you use to bypass the relays is the second ?.
-
Do a search on ebay for a 2-wire Mini DC5V-120V Voltmeter LED Panel 3-Digital Display Voltage Meter UK, they are small but you will have to mount it somewhere where water can not get in the back of it ( good idea to fill the back up with hot glue after plug has been connected ), also always have a small fuse inline with the red lead ( just in case). A 2 mode switch idea will defo be possible but may require a bit of experimentation to get it to the values you want, it will involve setting the dials to the settings you require then disconnecting the pots and measuring the resistance of each pot/dial, this information can then be use to use fixed resistors and a switch. If each pot only has 2 wires then this will be straight forward but if they have 3 wires it may be more trouble than its worth.
-
with 24v battery and the same controller and ratio then nothing will change, To get more acceleration you will either have to lose a bit off the top end via ratio ( but this will also increase the torque and may not be very desirable/controllable ), or increase the voltage to 36v , this will also increase the top speed and you can then charge the ratio to slow it down again but this can cause the same problems as above, you will prod also have to replace the controller to a 36v one so you will need to know what is the current limit on the 24v contoller so you can either match it or have a higher current limit . Or the last option is to increase the current limit on your exsiting controller and change the ratio to make it a bit faster , but im not totally sure if this can be done on the older oset controllers. but no matter what way you go you may have more problems with the motor over heating
-
yes a 8 amp charger will reduce the charge time.... I think you have a few cells with in the battery that have got very out balance and thats why it is cutting out at 51 volts it should cut out at around 44v for a 14s and around 41v for a 13s. Worst case scenario is that there a few duff cells in the battery. this can be repaired, but you do need to check the voltage output of your charger it should be 58.8v if its lower then you battery will never charge to full capacity anyway.
-
ok so if your battery is only getting to 56v then this is way to low, the only thing I can suggest is to leave the battery on charge for at least 24hours then measure the output to see if this increases the battery voltage... i advise charge in a fire safe area i.e outside some where, dont charge indoors for this long!!. final fully charged voltage should be 58.8v
-
It sounds like you have a battery bms problem. out of interest what do your charger say is the output voltage is?, as 56v is to high for a 13s battery and to low for a 14s battery, this can also be caused by the battery bms ( not fully charging the battery ) but it may be the wrong charger.
-
the OP said he had little electrical knowledge, yes load test charger would be the next step if it was the correct voltage coming out of it. personally I would just monitor the charge current and charge voltage over time then discharge the battery with a know load and measure the capacity and C rate. IR can change so much with temperature so it not always a good way to go with sla but good enough if you had them from new and knew what the IR was from new and at a specific temp.
-
1: you need to measure the voltage at the batterys , when charging and when not charging, full battery should read around 39v ( without charger connected ), a flat battery will read around 36v or even lower 2: measure voltage out of the charger when not connected to battery should be around 39v, for 3 sla batterys this is a starting point to get to the bottom of the problem
-
remove the cover clean hole and fill the hole with jb weld dont worry about trying to fit the bolt back on as it serves no purpose. just make sure that when the cover is back on that the coils dont rub or hit any jb weld on the inside
-
yes there is but i dont know if this will help and i dont know if the cost of a gamble would be worth it, Im not sure what controller is on that model oset but some controller you can turn down the current, if you can only turn down the speed this will not do the trick. if someone can post up the peak current of these bikes it would then be easy to source a battery for them. you can have a look at power tool batterys these tend to be high drain and a cheaper option to boost-bike battery's , this is acually a good option on the smaller bikes, but not so good on the bigger bikes.